

In contrast, the term subtractive manufacturing appeared as a retronym for the large family of machining processes with material removal as their common process. The umbrella term additive manufacturing (AM) gained popularity in the 2000s, inspired by the theme of material being added together ( in any of various ways).
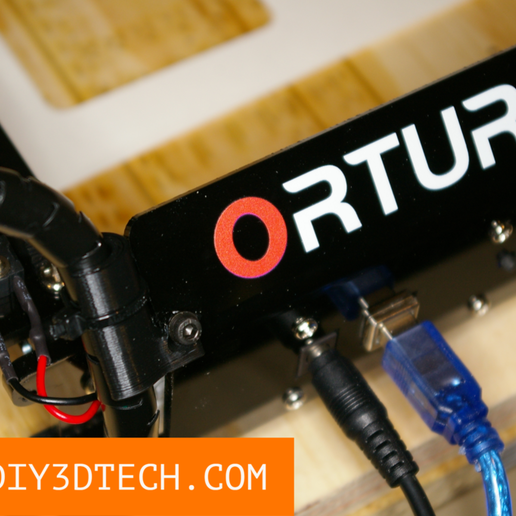
Fused deposition modeling (FDM), which uses a continuous filament of a thermoplastic material, is the most common 3D printing process in use as of 2020. One of the key advantages of 3D printing is the ability to produce very complex shapes or geometries that would be otherwise infeasible to construct by hand, including hollow parts or parts with internal truss structures to reduce weight. As of 2019, the precision, repeatability, and material range of 3D printing have increased to the point that some 3D printing processes are considered viable as an industrial-production technology, whereby the term additive manufacturing can be used synonymously with 3D printing. In the 1980s, 3D printing techniques were considered suitable only for the production of functional or aesthetic prototypes, and a more appropriate term for it at the time was rapid prototyping.

It can be done in a variety of processes in which material is deposited, joined or solidified under computer control, with the material being added together (such as plastics, liquids or powder grains being fused), typically layer by layer. 3D printing or additive manufacturing is the construction of a three-dimensional object from a CAD model or a digital 3D model.
